Recent prosecutions: Business fined £1.6m after fatal crushing incident
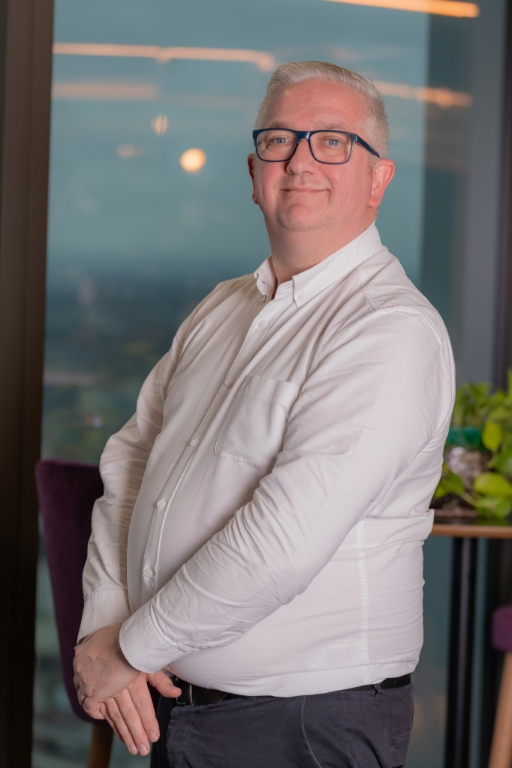
Ian Dunsford
December 13, 2024
2
min read
A business received a £1.6m fine and over £23,000 in costs following a crushing incident that took the life of a 24-year-old man.
The young worker was assisting while a lorry-mounted crane lifted sections of a Mast Climber Work Platform. The crane’s lifting sling, which was found to be out of date, snapped and caused the load to fall.
A police and Health and Safety Executive (HSE) investigation found that the company had not adequately planned the lifting operation and had neglected to implement safe exclusion zones. They also failed to have safe systems in place to regularly inspect crane accessories and dispose of expired equipment.
The HSE principal inspector said: ‘This tragic incident led to the wholly avoidable death of a young man. This death could so easily have been prevented if [his] employer had fulfilled its statutory duty to plan and manage the risks associated with lifting equipment and lifting operations.
‘[His employer] failed in its duty of care to all its operatives…in the way it planned and implemented the lifting operations and the slack customs and practices it allowed to become part of the safety culture with regard to lifting.’
LOLER: Ensuring safe lifting practices across your business
Lifting operations are covered by the Lifting Operations and Lifting Equipment Regulations 1998 (LOLER). LOLER applies to all workplace lifting operations and equipment, such as cranes, forklifts, hoists, slings, and chains.
The law requires that all lifting operations involving lifting equipment must be:
- Risk assessed and planned by a competent person.
- Appropriately supervised.
- Carried out in a safe manner.
- Properly secured to prevent slipping or falling during lifting.
LOLER also states that all lifting equipment should be strong, stable, and suitable for the job. In practice, this means that it is:
- Fit for its intended purpose.
- Appropriate for the task.
- Clearly marked with its safe working load (SWL).
- Regularly inspected by a competent person.
Training your employees on safe lifting techniques is key to LOLER compliance. By building hazard awareness, you can take a proactive approach to risk management, boost accountability, and prevent safety incidents.
Through targeted training, your team should understand:
- Their legal responsibilities under LOLER and how to apply them to daily tasks.
- The risks of improper use of lifting equipment and how to avoid them.
- The correct use of key equipment like forklifts, cranes, and slings in line with the manufacturer’s guidelines.
- How to identify and act on unsafe practices, including overloading, improper rigging, and unstable loads.
- The limitations of the equipment they use, such as safe working loads (SWL).
- How to carry out on-the-spot and scheduled equipment checks and correctly report issues.
Confidently raise safety standards
As an employer, it’s your responsibility to provide safe lifting protocols and equipment, ongoing maintenance, and adequate staff training. Opus can support you at every stage – from initial risk assessments and acting as a competent person to improving your team’s safety knowledge.
To learn how we can solve your safety challenges, get in touch on 0330 043 4015 or email hello@opus-safety.co.uk.
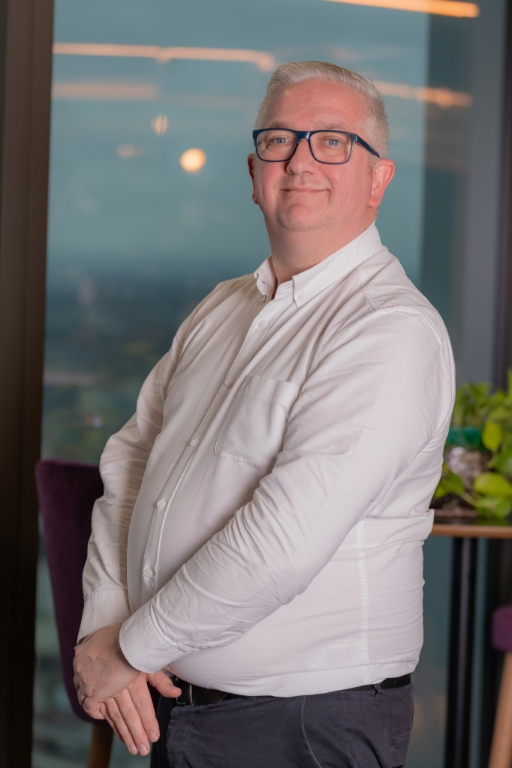
Ian Dunsford
December 13, 2024
2
min read