Recent prosecutions: Crushing incident costs manufacturing company £60,000
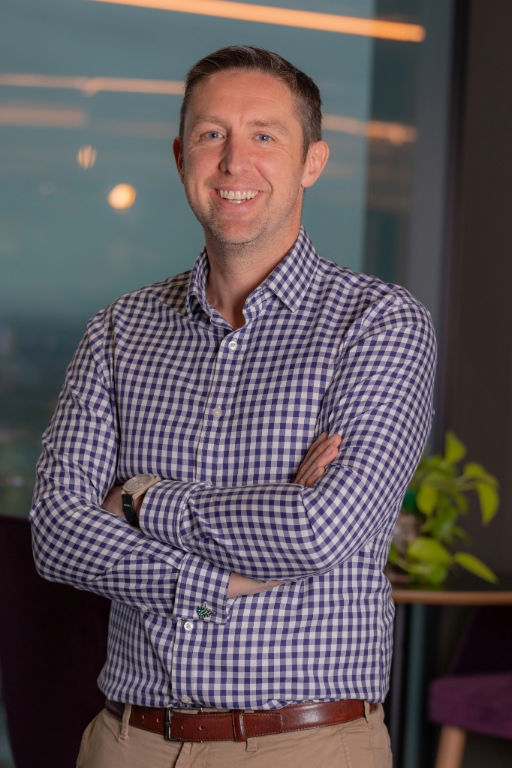
John Southall
February 11, 2025
2
min read
A manufacturing business was hit with a £60,000 fine following a crushing incident that caused a new employee to lose his lower leg.
The recently hired supervisor was working a night shift when an 800kg pallet fell from an overhead crane onto his legs. A Health and Safety Executive (HSE) investigation revealed that the pallet was not securely fixed to the crane’s lifting chains, leaving it unsupported while in transit.
The employee endured a seven-week hospital stay, during which his lower right leg was amputated and two toes on his left foot were removed.
The HSE found that the manufacturing company had failed to establish a safe system of work that would have allowed the pallet to be safely lifted from its reinforced concrete cast. Neither the injured employee nor his co-workers had been trained to correctly extract the pallet.
The HSE inspector said: ‘This incident could so easily have been avoided with the correct instruction and implementation of an agreed safe working procedure. Amber Precast Ltd left its employees to work out their own methods of completing the pallet removal task, instead of providing them with suitable training and equipment so it could be done safely every time.’
Establishing safe systems of work
A safe system of work (SSoW) is a set of procedures that help employees complete tasks with minimum risk. Created by health and safety professionals, SSoWs identify hazards, implement controls, and ensure regulatory compliance. They’re essential to preventing safety incidents and protecting staff, customers, and visitors in your builder’s merchant.
SSoWs vary depending on the job in question, but a well-structured framework will typically cover:
- Risk assessments to pinpoint potential hazards and identify safety threats associated with your business’s daily operations.
- Clear work procedures that outline safe methods for common tasks such as manual handling, vehicle loading, and forklift use.
- Staff health and safety training to ensure staff understand compliance fundamentals and follow correct procedures.
- PPE requirements for any given task, including safety boots, hard hats, and hi-vis clothing.
- Incident reporting processes to encourage employees to document near misses, accidents, and safety breaches.
- Inspection schedules outlining the frequency of equipment checks and maintenance routines.
- Emergency response plans detailing fire safety, first aid, and incident response procedures.
Raise safety standards with Opus
Clear processes and compliant working practices can save lives. For proven expertise across risk assessments, safe systems of work, and staff training, speak to your Opus Safety consultant on 0330 043 4015 or email hello@opus-safety.co.uk.
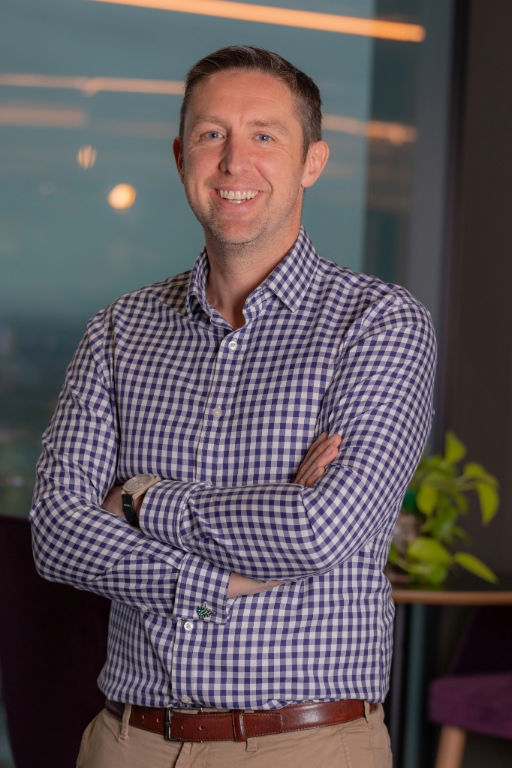
John Southall
February 11, 2025
2
min read