Tackling the builders merchant sector’s top six hazards
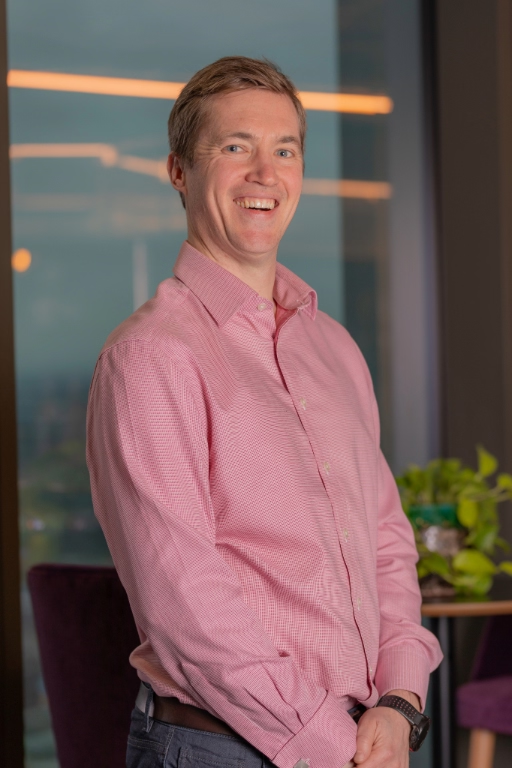
Ian Hatherly
February 11, 2025
3
min read
While each builders merchant has site-specific safety challenges, every operation should take action on the industry’s six most common compliance threats.
Too often, everyday risks – from loud environments to poor lifting techniques – become ‘business as usual’ working practices that leave staff vulnerable to job-related accidents and ill health. Recognising common safety issues helps you protect your team and prevent the financial fallout of incidents, penalties, and civil claims.
In this blog, we share the merchant sector’s top health and safety hazards – and expert tips on how to eliminate them.
1. Slips, trips, and falls
Slips, trips, and falls continue to be the single biggest cause of workplace accidents, despite being easily prevented with basic hazard awareness and a clean-as-you-go culture.
A comprehensive risk assessment highlights common hazards and identifies the most effective controls to manage them. Your assessment should cover make-or-break compliance areas – such as housekeeping routines, walkway access, and branch design and maintenance – and address common hazards, including:
- Poorly installed and uneven flooring, including loose tiles or sudden changes in height
- Inadequate lighting
- Loose cables, wires, and strapping
- Stock, supplies, and boxes positioned in walkways
- Protruding machinery footings and display units
- Spills and wet surfaces
2. Manual handling
Manual handling involves any activity of lifting, lowering, pushing, pulling, carrying, holding, or moving an object that requires physical labour. Health & Safety Executive (HSE) stats show it was linked to 17% of UK non-fatal workplace injuries in 2023/24 – but with simple safety measures, you can effectively head off incidents and compliance issues.
- First, conduct a risk assessment to eliminate or reduce the need for manual handling.
- Use the three-step ‘Avoid, Assess, Reduce’ methodology to pinpoint the best approach to transporting any load.
- Consider solutions such as using mechanical lifting equipment, changing the physical space to ease movement, and breaking down the load into smaller quantities.
- When manual handling is unavoidable, employ the TILE technique to identify hazards from all sides - posed by the Task, Load, Individual, and Environment – and plan safe, compliant methods of movement.
3. Machinery and vehicle risks
HGVs, forklift trucks, and heavy machinery bring speed and efficiency to your business. However, they’re the root cause of thousands of workplace accidents each year. Small but significant safety upgrades can make a life-saving difference.
- Separate pedestrians from vehicles by implementing barriered walkways between foot traffic and transport routes. Use zebra crossings where paths intersect.
- Introduce pedestrian-only gates to prevent people from using vehicle entrances as shortcuts.
- Enforce speed limits with clear signage and speed bumps to control vehicle movement.
- Minimise reversing by establishing one-way systems.
- Mandate seatbelt use for all drivers, regardless of vehicle type.
- Create designated loading zones to ensure a controlled, safe environment for deliveries, loading, and unloading.
- Take a zero-tolerance stance on machine guard tampering, backed up by clear rules on interacting with guards, raising safety concerns, and responding to emergencies.
- Create a pre-use machinery checklist, covering visual inspections for wear, damage, and signs of tampering.
- Revisit your machinery and workplace transport risk assessment whenever you introduce new procedures, equipment, or staff.
4. Falling objects
According to 2023/24 HSE figures, 10% of injured employees in the UK were struck by a moving object. Whatever your branch size, it’s essential to safeguard staff from the risks of products and materials being stored, stacked, and moved on your site.
- Secure shelving and racking to reduce the risk of collapse, ensuring units are correctly installed and regularly inspected.
- Follow best practice when stacking materials, placing heavier items on lower shelves and avoiding overloading.
- Use load restraints such as netting, straps, or edge protectors for products stored at height, particularly loose items like pipes and timber.
- Equip staff with appropriate personal protective equipment (PPE), such as reinforced safety boots and hard hats.
- Train employees on proper lifting, stacking, and securing methods.
- Clearly mark storage areas and restrict access during loading or unloading.
5. Exposure to hazardous substances
All businesses use hazardous substances – from cleaning products to corrosive chemicals. Under the Control of Substances Hazardous to Health (COSHH) Regulations (2002), you’re legally obliged to identify and reduce their risks and regularly monitor your control measures. Regular risk assessments, compliant labelling and storage practices, and consistent staff training are key.
- Conduct a COSHH risk assessment to locate harmful materials and evaluate their impact on the people exposed to them. Substances may include paint, bleach or fine dusts and fumes from welding, sanding, or cutting.
- Store chemicals and hazardous materials in a designated area and in their original containers.
- Ensure that storage areas are well-ventilated, secure, and situated away from ignition sources and direct sunlight.
- Store incompatible chemicals separately at a distance of at least three metres. Acids and alkalis should be kept on separate shelves.
- Store only the minimum required amount of chemicals on-site.
- Use secondary containment measures, such as spill trays or bunds, to prevent leaks and spills from spreading.
- Train your team on correct chemical handling and protection, including reading safety data sheets (SDS), using appropriate PPE, and maintaining adequate ventilation.
6. Noise and vibration
Noisy work environments and vibrations from tools and machinery can lead to ongoing health issues, including hearing damage and hand-arm vibration syndrome (HAVS). A proactive approach to safety can protect employees from long-term medical concerns.
- Assess noise levels using workplace monitoring and provide hearing protection where required.
- Limit exposure to loud equipment by rotating tasks and enforcing quiet zones where possible.
- Use anti-vibration tools and handles to reduce the impact of power tools such as saws and drills.
- Correctly maintain tools to reduce noise and vibration.
- Provide ear defenders or plugs for high-noise areas and anti-vibration gloves for staff who frequently use tools and machinery.
- Train staff on safe tool handling and recognising early signs of noise- or vibration-related health problems.
Solve your sector safety challenges with Opus
If you have questions about safeguarding staff from common workplace hazards, speak to an Opus Safety consultant. Our tailored risk assessments have helped hundreds of builders merchants protect their people and premises.
Get in touch on 0330 043 4015 or email hello@opus-safety.co.uk.
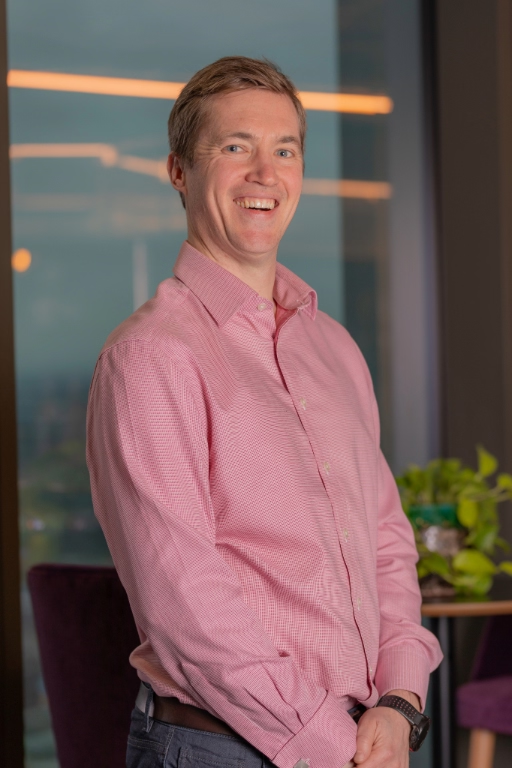
Ian Hatherly
February 11, 2025
3
min read