Training, checks, and a strong safety culture - how to stamp out unguarded machinery risks
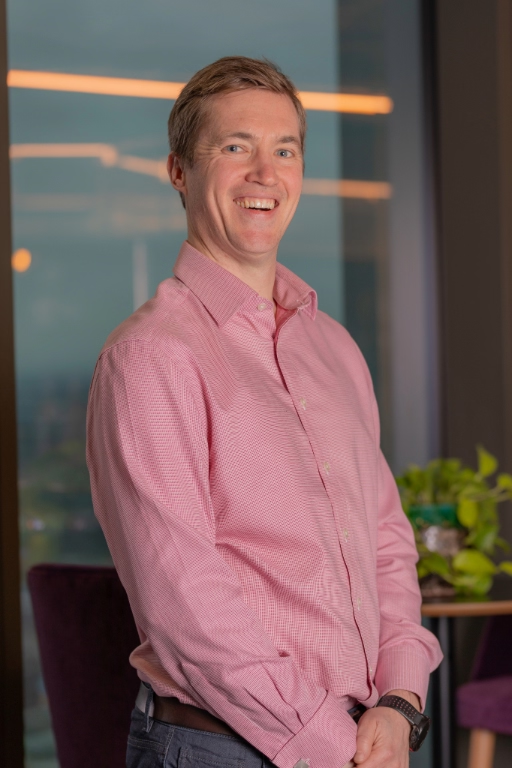
Ian Hatherly
August 28, 2023
4
min read
The dangers of unguarded machinery are well documented, with both workers and business owners paying the high price of poor health and safety practices. Most recently, an employee at a manufacturing company was paralysed from the chest down after becoming entangled in a CNC machine’s rotating saw.
A Health and Safety Executive (HSE) investigation found the machinery guards had been disabled, and the employer had failed to take effective measures to prevent access to dangerous machine parts. The company was ordered to pay £18,000.
According to 2022/23 HSE statistics, contact with moving machinery is the fifth most common cause of workplace fatalities in the UK. Guards play a critical role in protecting operatives from hazardous equipment – but rely on correct training, frequent risk assessments, and a robust safety culture to work effectively.
Here’s how to establish a safety-first mindset when using machinery.
Communicate the importance of machinery guards
Machinery guards are essential safety features that protect workers from dangerous moving parts. With many machine-related injuries, guards have been removed or tampered with to allow free access to equipment or achieve perceived production efficiencies.
Removing or overriding guards – or operating machinery without them – violates health and safety laws that can result in serious injuries and fatalities, fines and legal action, and insurance liability issues.
Guards should be properly installed and appropriate to the type of machinery in use. Common types include:
- Fixed guards are permanently attached to machinery, creating a physical barrier between operatives and the machine’s hazardous parts.
- Interlocking guards automatically shut down machinery when the guard is opened or removed.
- Light guards – or light curtains – use infrared beams to detect hazards. The machine stops immediately if a worker interrupts one of the beams.
- Adjustable guards can be repositioned to suit different-sized materials, while providing adequate safety protection. Similarly, self-adjustable guards automatically adapt to the workpiece’s dimensions as its fed into the machine.
Training your team – from senior managers to supervisors to shift workers – on the importance of machinery guards is a core component of your health and safety programme. Use a blend of online training, toolbox talks, and on-the-job coaching to consistently reinforce key messages. Headline topics should include:
- Machinery risks and safe operation
- Guard types and their purpose
- Identifying and reporting issues
- Following emergency procedures
- Taking a zero-tolerance approach to machine tampering
Conduct daily checks and regular risk assessments
On top of staff training, regular risk assessments and safety checks are your quickest route to compliant machine use. Keep machinery fit for purpose with a comprehensive safety audit, routine maintenance schedule, and stringent pre-use checks.
- Include machinery and guards in your risk assessment process.
- Create a pre-use checklist, covering visual inspections for wear, damage, and signs of tampering. Test key components, locks, and emergency stop mechanisms.
- Establish safe work procedures that outline how to interact with guards, flag safety concerns, and respond in an emergency.
- Introduce a lockout process for maintenance and repair work, isolating machinery at its energy source and preventing unexpected startup.
- Revisit your risk assessment whenever you make changes to procedures, equipment, or staff.
Simplify machinery safety with QR codes
Technology can introduce much-needed consistency to your H&S programme, empowering staff to access and follow site rules and develop deep-rooted safety behaviours. For example, the Opus Compliance Cloud platform uses QR codes to unlock pre-use machinery checks.
Workers quickly scan the code before operating a piece of equipment, running through compulsory safety spot checks and ensuring guarding is intact and fully functional. Data is captured in real-time to highlight training or machinery issues, boost hazard reporting, and standardise safety surveys.
Work with Opus to prevent machinery-related incidents
We’ve supported employers across the UK to prevent accidents and create a more safety-conscious workforce. Talk to our team about tech-enabled H&S programmes and training strategies for your business.
Get in touch on 0330 043 4015 or email hello@opus-safety.co.uk.
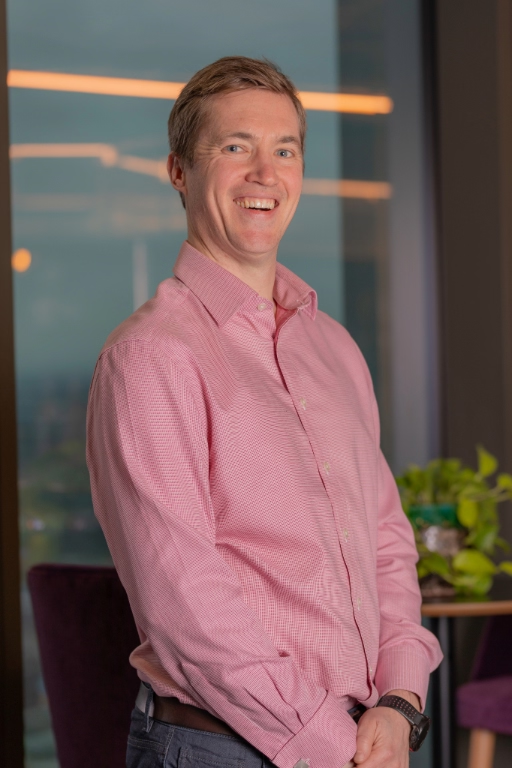
Ian Hatherly
August 28, 2023
4
min read